Derek Sharp of TreeHouse Drums is a man interested in roots and what they produce. You can interpret this statement in a couple of different ways. For one, you could look to the origin of his company’s name, taken from a treehouse he built his wife years ago when they were kids living across the street from one another. Taken in another light, Derek is zealous about the process, from start to finish, of taking a tree and transforming it into a unique, beautifully made instrument. Either way you look at it, Derek’s a man of passion and dedication, two qualities central to his company.
TreeHouse Drums has been crafting custom sets for the past fifteen years. Operating out of the “Drumgeon” (their workshop) in Topeka, Kansas, the company consists of Derek and a small but dedicated band of employees with keen eyes and ears for the best looking and best sounding drums they can possibly produce. Not content as a one-trick pony, TreeHouse is unique as a custom shop who caters not only to artists, but to academic institutions as well with its array of custom-made band, orchestra and world instruments.
We caught up with Derek to discuss his process, his interests, and how a Whoopi Goldberg film inadvertently acted as the inspiration for one of the most ornate snares we’ve ever seen.
You have one of the widest selections of available woods for your drums I've seen for a salon shop. What is your process for selecting which woods to use, and how do you source them?
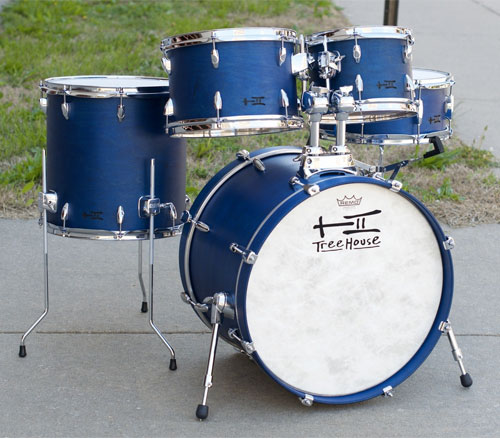
I'm curious about how various species look and sound and have tried dozens over the years. Besides the awesome visuals of colors and grains you see in different woods species, I look for different types of sounds. I tend to agree with a notion put forth by Greg Gaylord which is that among wood species for drum building, there are three broad categories: American "soft" hardwoods (fir, pine, sycamore), American "hard" hardwoods (oak, ash, birch, maple), and "exotic hard" hardwoods (wenge, padauk, bubinga). Now I know that these are generalizations, but overall, the first category offers warm, round, mellow sounds, the second offers more bite, attack, and presence, and the third is brighter, higher and offers more crack. That said, the wood species is just one ingredient in a long list of what all goes into making a drum which needs to be kept in mind when designing your ultimate sound.
What are some of your favorite finishes? What are some materials you're interested in working with for a new finish?
My favorite medium is simply applying dye directly to the shell then sealing with oil and finishing with hand-rubbed wax. This system is easy to reproduce and to repair. I'm looking forward to bringing to market some ideas I have for cloth-clad drums...think Khaki battle worn canvas like a French Legionnaire returning from the field.
Your best-selling product is your nesting drum. How did you originate the idea? Can you explain how they function? How do you retain tonal quality with a latched drum shell?
The Compact Nesting Kits were designed with input from a few artists in New York City. I live in Kansas with a Suburban and a Minivan driving the plains-these guys live in apartments, don't own cars, and use subways & taxicabs to get their drums around. One of the prime movers, Danny Young, took a tape measure to the turnstiles in the subways so we'd know how much room we had to work with. Another artist, Shannon Ford, actually hailed a NYC cab, popped the trunk, and figured out its clearance. I took 9 months measuring different configurations, experimenting with the joinery of the split shells, and finally brought the first kit to market in March of 2013.
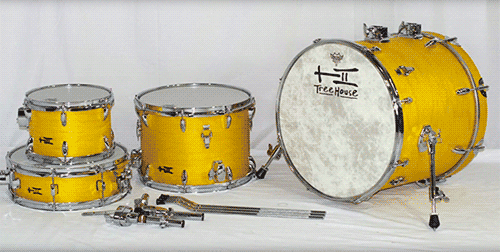
I needed something that sounded great-I mean, it's neat to nest [the kit] like Russian Dolls, but if they're weird, they'd just be a gimmick. These drums are 100% maple (or "Vintage" mahogany/poplar) and fitted with proper bearing edges. They’re sized so the toms fit into each other then fit into the bass. This stacking happens with the heads remaining attached: you open 3 or 4 latches to lift off a "lid” of 3 or 4 inches which has lugs, head, and rim all attached. You nest the smaller drum in the larger, replace the lid, then latch everything shut. Customers can opt to add cymbal arms & an accessory arm to the bass shell. It [a Nesting set] takes about one minute longer to set this up than a regular drumset. At the separation seam joint, we install a seam lip [a reinforcing ring hand-shaved to custom fit the lid]. There's no rattle, no buzzing, no weirdness of the sound. I haven't tested these drums on any high-tech electronics lab equipment, but as a drummer of 30+ years, I can honestly tell you that I hear no difference between one of these split shells and one uncut.
A number of your endorsees are universities and high schools, not typically seen on a custom shop roster. How did you develop relations with academic institutions?
Two of the three of us that make drums for TreeHouse were percussion majors in college. We were annoyed by the logistical challenges of positioning standard huge concert bass drums on upright stands near snare/woodblock/cymbal set ups for multi-percussion pieces in percussion ensemble. This lead to the development of our Concert Bass Toms. Our main marketing effort out of the store is through providing TreeHouse drumsets at regional University jazz festivals. There, middle school, high school, and college drummers/directors/bassists/etc. can play, see, and feel these drums in person. That exposure has lead to several school and US Military sales.
How did you begin developing your lines of marching, concert and world drums?
A friend of mine, David Macejka, is heavy into the Renaissance Faire world. He turned me on to Tupans which are
East European ethnic rope-tuned bass drums. Such drums go by several name and are actually used in many countries
in Europe and the Middle East. Anyway, they're double-headed drums with a boomy low bass side played with a mallet
and a bright ring-y treble side played with a switch (like a long chopstick). From there, I looked at 3" deep
shell scraps I had in several diameters. These developed into what I call Practice Tenors, which are like the
marching quads we played in high school and college, but designed to rest on a snare stand instead of on a
shoulder harness. They're more portable than "real" Quads or Quints, lighter, cheaper, and can be used for
practice, composition, rehearsal, or in the stands indoors. Also, I've been fascinated by how different wires
such as guts, cords, springs, cables, etc make such different sounds on snares. It's a fairly easy transition
to install some of these on a snare to make it appropriate for symphonic or concert use.
Many players are enamored of custom shop quality but intimidated by the price. How is the pricing tiered for TreeHouse?
Yeah-the Almighty Dollar Sign! TreeHouse existed for a couple of years before the first price list was even published. There were so many options, I had 30+ lists to cover all the options! Too much. I had to strike some averages and group things together, so I published a three-tiered pricelist. I also introduced a new price category called the ACADEMY series consisting of Concert Toms, Concert Bass Toms, and Practice Tenors. These are packages for everyone, but designed with pricing within reach of schools. The same quality of workmanship and materials go into these drums as all of my drums, but with fewer cosmetic options to keep pricing as low as possible.
On another note, TreeHouse is located in the building in which the owner operates a drum-n-guitar shop, so facility overhead is zero. I'm in the Midwest where most everything (overhead/cost of living) is a little less than on the coasts and sole distribution is through one store, so pricing lands less than many high-end, established custom builders.
When did you start working with metals for your snares? What led you to choose working primarily with hammered brass?
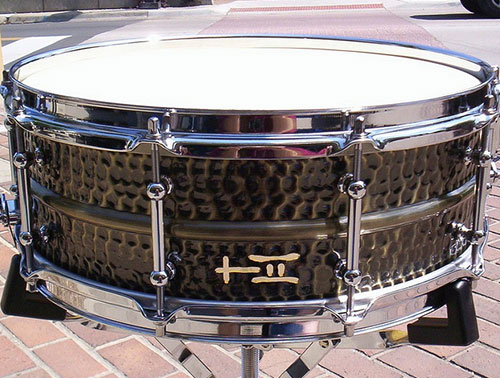
Starting in 2004, I began using a variety of hammered brass shells. Brass has been a historic score for snares-those historic Black Beauties by Ludwig (actually, they called them the DeLuxe model), Slingerland and Leedy (Black Elites) starting in the 1920s were brass shells. My favorite drumsmith today, Adrian Kirchler, uses this fantastic material for his best work. There's a warmth and a great pop there. Part of why some metal snares are "ringy" or too bright-sounding for some folks is due to a construction feature where the inside walls of the drums are smooth. Roughen them up a bit...say...hammer a bunch of dimples in them, and the downward rush of the air column which is displaced when the drum is hit is disturbed. That is, the air moves more randomly within the shell of a hammered metal drum than one with a smooth wall. This slows things down and removes reflection so that we hear a warmer sound with relatively fewer high overtones. This isn't to say that highs aren't there (check out Bill Stewart playing with his hammered Ludwig snare with John Scofield), there's just a blossomed warmth to the drum's fundamental tone as well a more reserved version of highs. WOW, it's hard to describe sound in words!
Your custom mosaic glass finish is very detailed. How did you develop the concept?
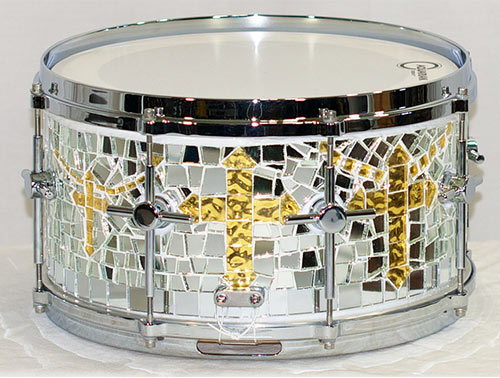
Taurus Lovely [the artist the drum was designed for] is one of the happiest people you'll ever meet! I'm blessed to have him on board with TreeHouse. When he was playing drums in the pit for the touring cast of the Broadway production of Sister Act (remember the movie w/ Whoopie Goldberg? It's a stage show too!), he wanted a snare that looked like what was going on onstage during the final act. The 14' Mary statue was turned around to expose her wearing a quarter-million hand-laid glass mirror tile mosaic garb as the nuns on stage shed their habits to reveal shiny sequin dresses. So, I became a dealer of a glass tile company to be able to afford all the tools, equipment, and supplies necessary to turn a snare drum into a disco ball. Along with the mirror tiles, I laid goldleaf-backed tiles in cross patterns across the drum as Taurus always wears a gold cross on a chain. Somewhere around 750 pieces of individually hand-cut hunks of glass along with commissioned chrome-over-solid brass cross-shaped lugs, plus one and a half years of evenings and weekends brought this 16-ply instrument to life.
TreeHouse Drums Official